Leading US automotive OEMAutomated bolt torquing
Challenge
At one of its North American facilities, the automaker assembles automotive seats on rails. During this process, the OEM faces several types of variance. The bolt positions vary due to manual pre-threading, a conveyor system designed for human operation, and inconsistent parts from suppliers. Furthermore, unstable lighting conditions pose challenges for traditional vision systems.
Outcome
The OEM has automated seven bolt torquing tasks previously deemed unfeasible with traditional automation methods by employing Universal Robots cobots integrated with the MIRAI system. Each MIRAI-equipped solution saves more than $200,000 per year. The automated systems handle variance in bolt positioning, lighting, and inconsistent components from suppliers with a nearly 100% success rate, resulting in improved production throughput and less manual intervention.
A leading automotive manufacturer runs four assembly lines for automotive seating production at one of their North American facilities. The assembly process involves several bolt torquing tasks. In these tasks, operators manually insert bolts into threaded holes as the seats move along the line. The seats then arrive in front of two robots that tighten the bolts. Automating this final step reliably with traditional robotic solutions or vision systems has proven challenging for three reasons:
- Manual pre-threading of the bolts and the use of a conveyor designed for human operation results in X, Y, and Z variance in bolt position relative to the robot. It was impossible to blindly position the robot tool over the bolts using hard-coded positions.
- Inconsistent components from suppliers and variance in part presentation make the use of traditional robots difficult.
- Unstable environmental lighting conditions result in unreliable execution of vision systems.
To address these challenges, the company collaborated with Micropsi Industries’ dedicated customer success teams to deploy seven robots equipped with the MIRAI AI-vision software and an automatic torque wrench at the assembly station. The integration of MIRAI was crucial and enabled precise alignment of the wrench with the bolts, accounting for variance in bolt positions and adapting to the environment in real time. Moreover, MIRAI effectively overcomes the limitations of traditional vision systems, performing reliably under varying lighting and part presentation conditions.
Today, MIRAI-guided robots are used on four lines for automated bolt torquing. With each MIRAI-equipped solution implemented, the OEM is saving more than $200,000 per year. The precision and efficiency of the automotive seating assembly process has been significantly improved with the implementation of the software. Overall, the AI solution has successfully enabled engineers to automate a process that was previously not feasible, with a setup time of less than two days and a nearly 100% success rate.
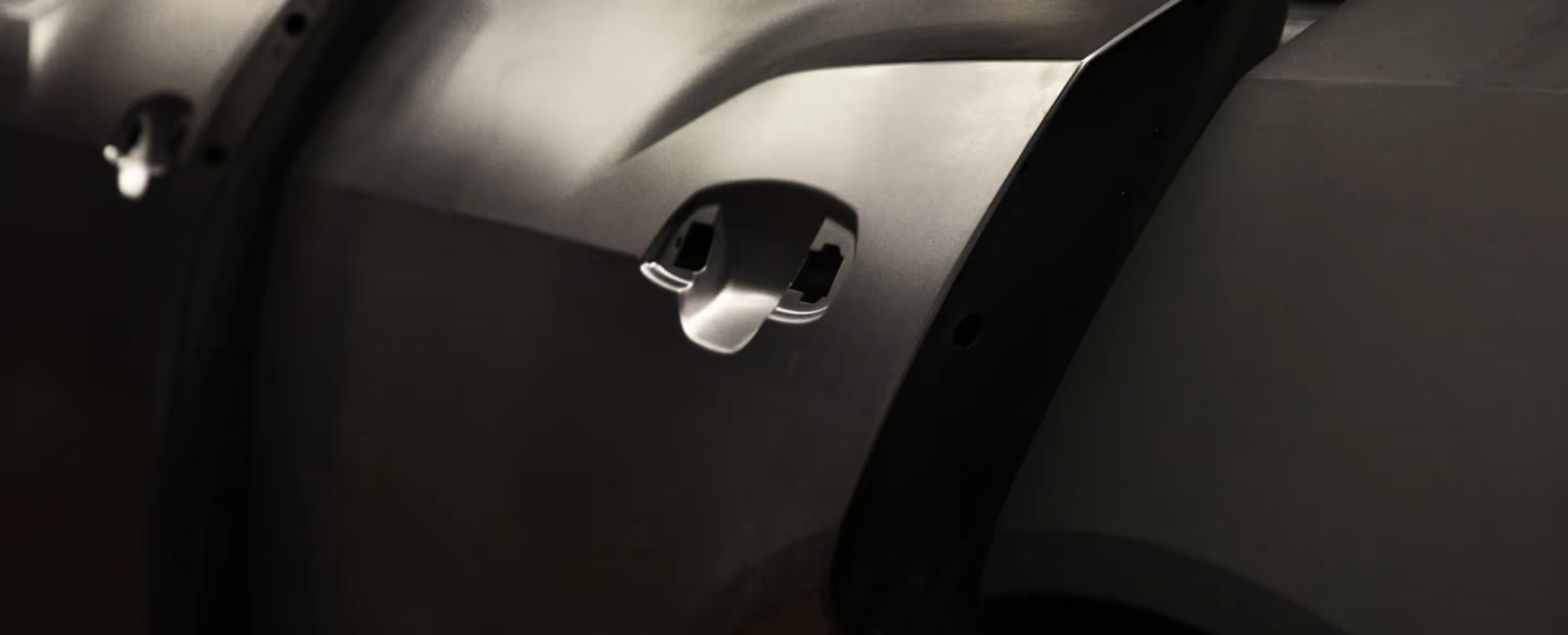
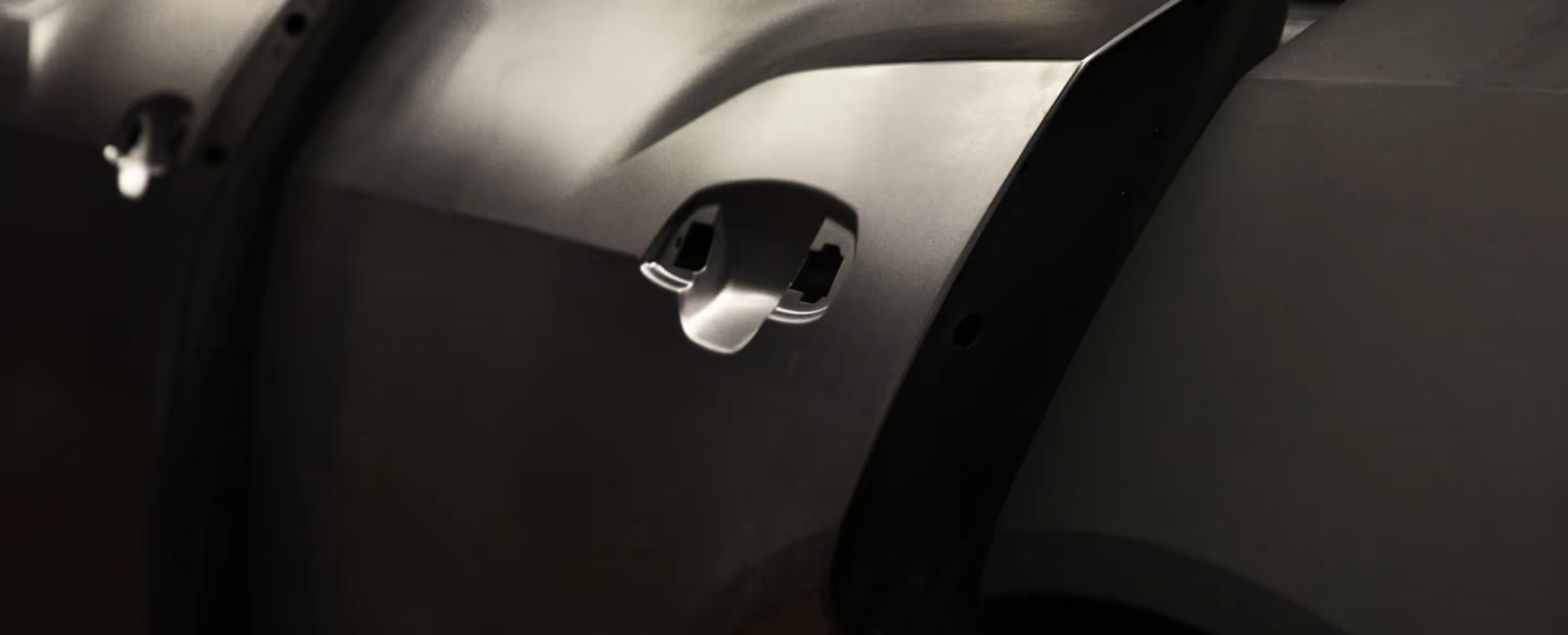