Siemens EnergyInsertion
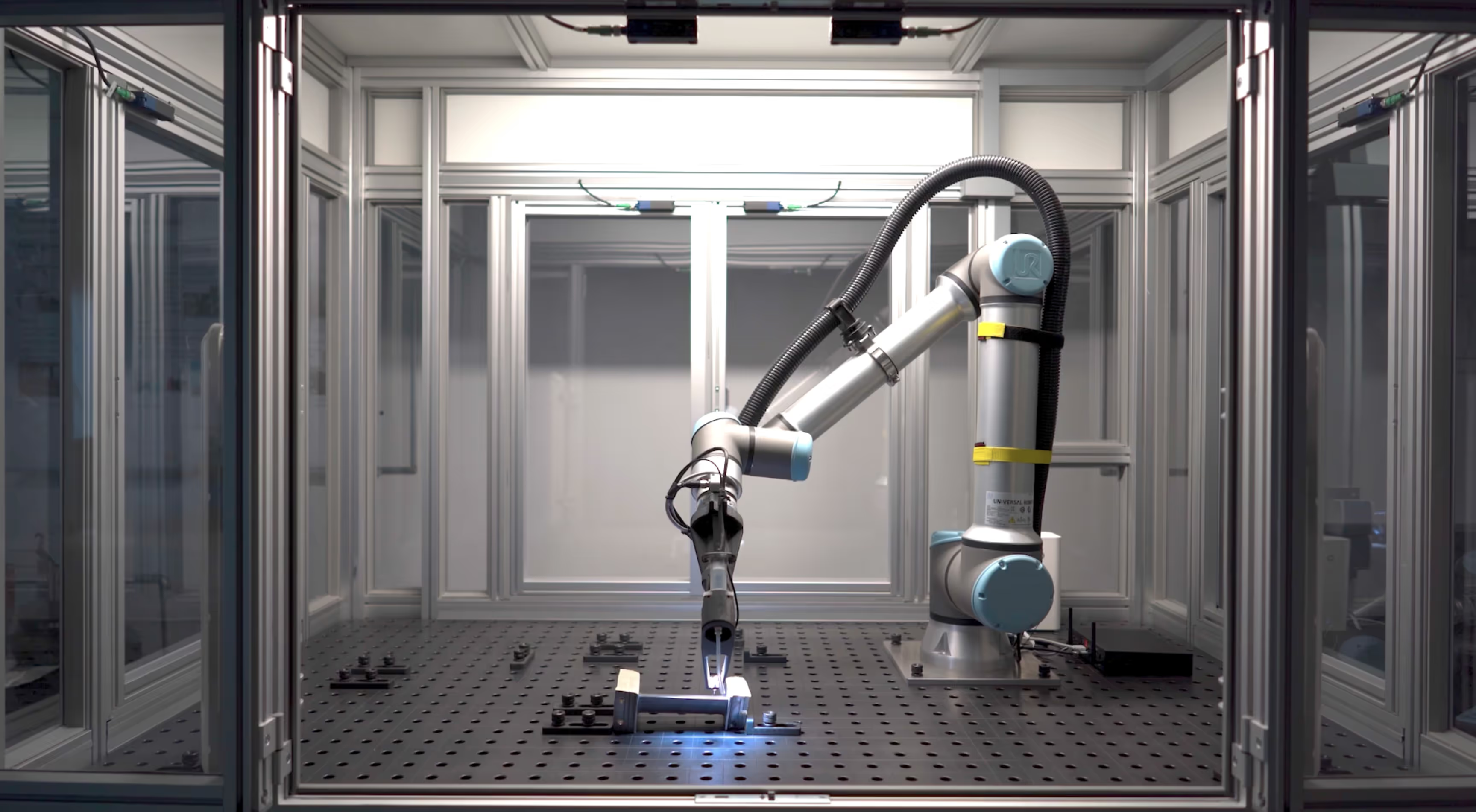
Challenge
In the refurbishment process, hundreds of tiny drillings along the surface of the vanes must be filled before surface treatment. This involves inserting a thin needle into every individual drilling and dispensing soldering paste. The task brings three main challenges: There is variance in the drilling position, variance in the shape of the vane, and variance in the condition of the vane.
Outcome
Thanks to the MIRAI AI-vision software, Siemens Energy is now able to automate the process step in the refurbishment of gas turbine vanes. An industrial robot equipped with MIRAI can insert the dispensing needle into the drillings of the turbine vane, overcoming variance in the drilling position, variance in the shape of the vane, and variance in the condition of the vane.
Siemens Energy, a leading energy technology company, intends to automate a process step in the refurbishment of a gas turbine vane. After four years of use (during operating hours), the vanes are reshaped and surface treated. Along the surface of the vanes are hundreds of tiny drillings, each roughly two millimeters wide. The drillings were used for air cooling during the vane’s previous use — when temperatures in the turbine get so hot that the vanes would melt without measures like air cooling and coatings. In the refurbishment process, the drillings must be filled in before surface treatment. This involves inserting a thin needle into every individual drilling and dispensing soldering paste. The dispensing task brings three main challenges:
- The drilling positions on the vane deviate due to temperature deformation of the vane during prior use.
- The soldering-paste dispensation is cumbersome, with hundreds of drillings to be filled. It takes hours for a human to fill them all.
- The vanes themselves come in different versions and different states of wear.
Thanks to MIRAI, Siemens Energy is now able to automate the process step in the refurbishment of gas turbine vanes. An industrial robot equipped with MIRAI can insert the dispensing needle into the drillings of the turbine vane, overcoming:
- Variance in the drilling position
- Variance in the shape of the vane
- Variance in the condition of the vane
During the overall automation task, the MIRAI system kicks in for the complex parts. MIRAI handles the movement of the needle from one drilling to the next drilling along the vane's edge as well as the precise insertion of the needle into the drillings. For its part, the robot’s native controller handles the dispensation of the soldering paste and other predetermined parts of the task. Training the MIRAI-powered robot took only a few days and was done by Siemens Energy engineers.
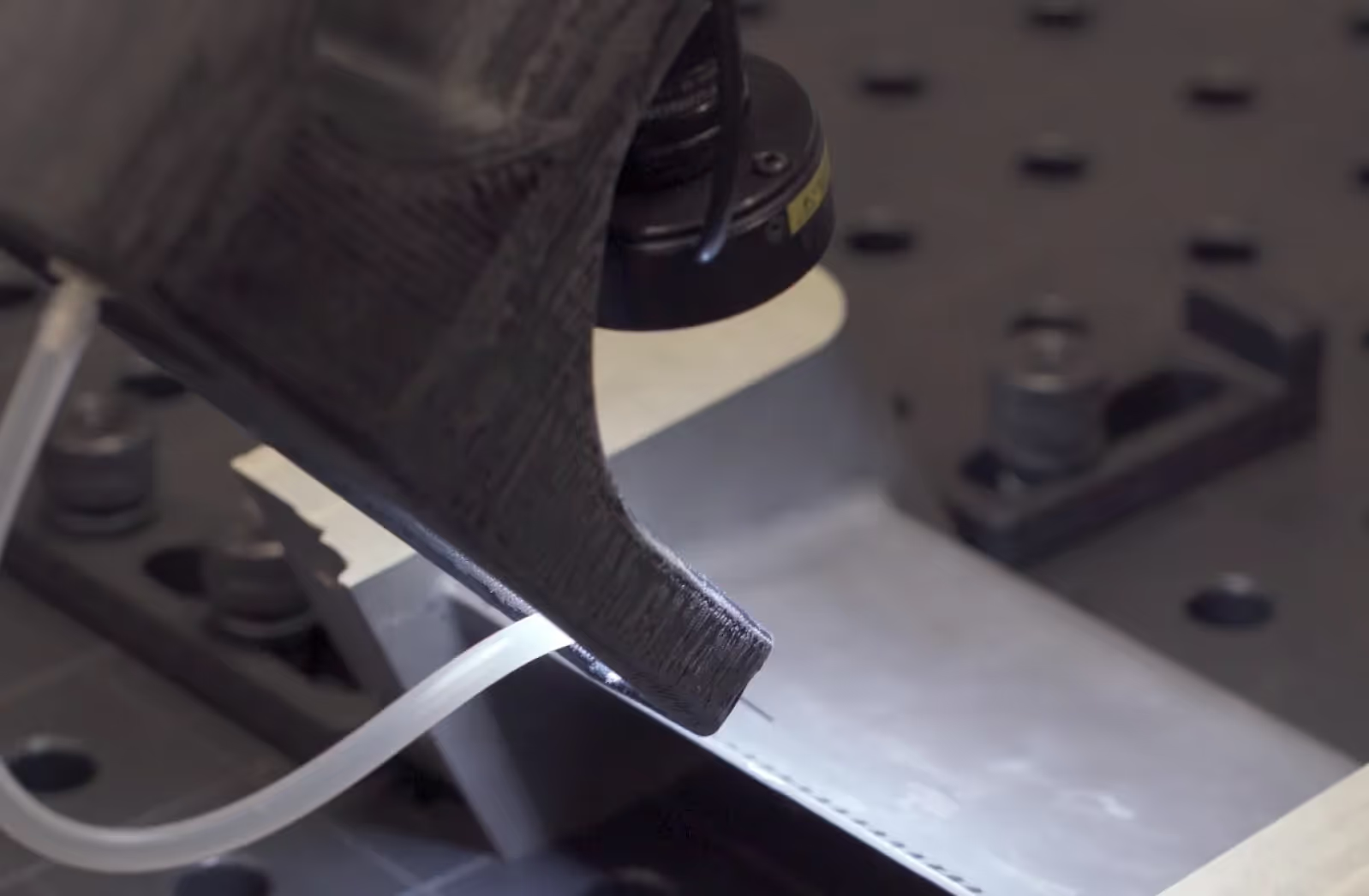
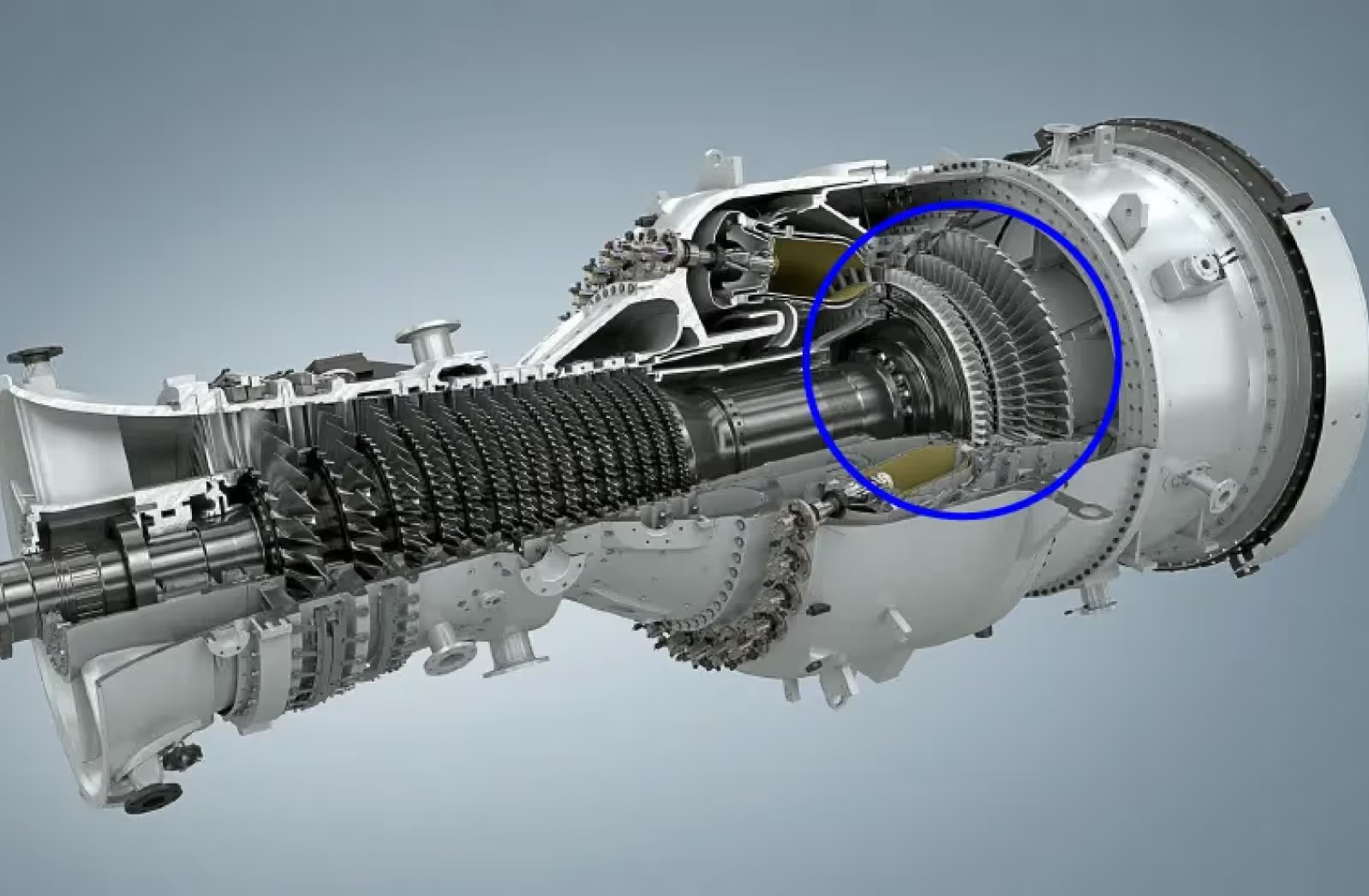
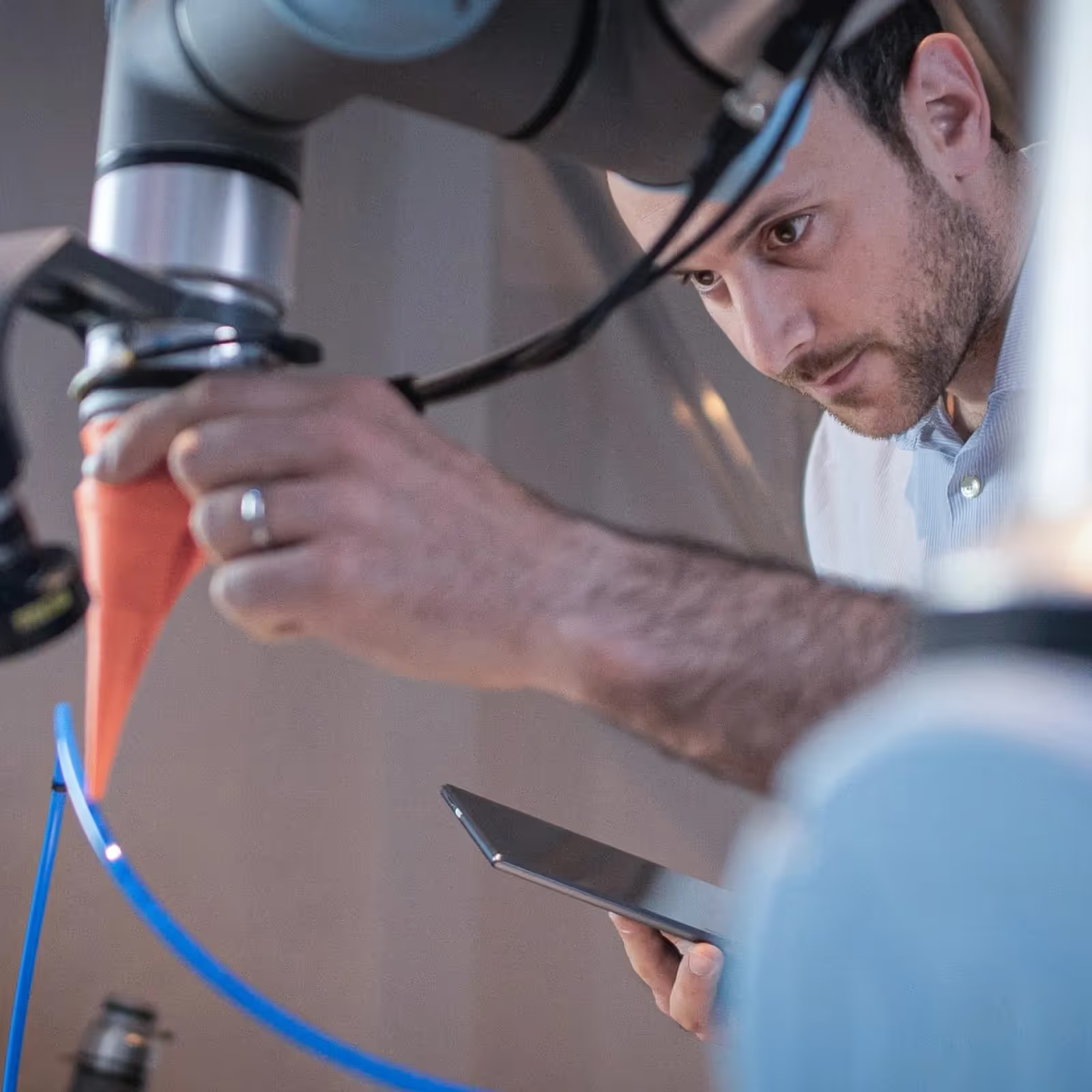
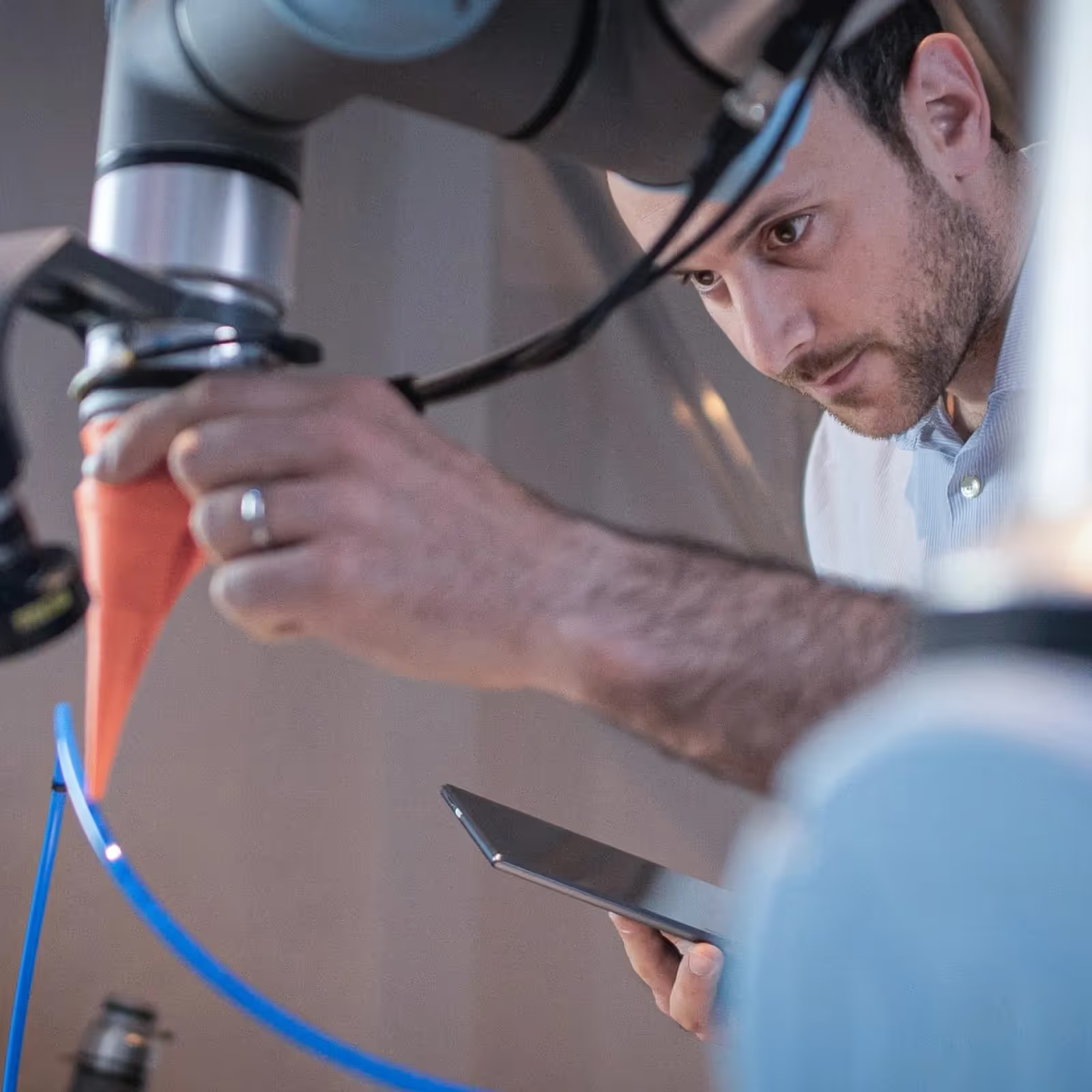